About Us
Techniche Engineering provides computational fluid dynamics (CFD) to broad range of engineering companies.
Techniche Engineering Private Limited is an ISO 9001:2015,18001:2015, 140001:2015 certified Indian consultancy with a global vision of ‘Safer World, Better World’ and with our core values, integrity, ingenuity, accountability and trust.
We are a team of expert simulation engineers that work on various industrial problems and have successfully executed CFD projects across the world. With more than a decades of experience, we are diligent to optimize your design issues and ensure that we have solutions that cater to the problems in various industrial domains such as oil and gas, refineries, power plants, marine, mining, renewable energy, automobile, healthcare, aviation and manufacturing industry.
TEPL has other engineering studies, services, trainings & audits-inspections related to Health-Safety-Environment (HSE). Our list of services includes QRA, FERA, EERA, HAZID, HAZOP, ENVID etc. We cater to the services related to process engineering in oil & gas, infrastructure, nuclear, chemical, fertilizers, pharmaceutical, manufacturing etc. We have widened our horizons by venturing in the environment services such as STP/ ETP installation.
Get A Quick Call Back
Services We Provide
Vapour Cloud Explosion Modelling
A vapor cloud explosion (VCE) results from the ignition of a flammable mixture of vapor, gas, aerosol, or mist, in which flame speeds accelerate to sufficiently high velocities to produce significant overpressure. VCEs are generally associated with the release of a sufficient quantity of flammable gas or vaporizing (flashing) liquid from a:
It Includes,
- storage tank
- process or transport vessel.
- piping system etc.
CFD study help to analysis vapor cloud developed due to release of flammable gas & overpressure generated after explosion.
Dust Explosion modeling
Dust explosions are a continuous threat in facilities producing combustible powders and dust as final and intermediate products. Combustible dusts are fine particles that present an explosion hazard when suspended in air in certain conditions.
The main objectives of Dust Explosion Analysis study are to:
- dentify the possibility of dust explosion for potential locations of the which can generate combustible dust leading to dust explosion.
- Provide design explosion loads (overpressure and its duration, drag load and impulse) for units and buildings.
- If explosion overpressures are found to be high then provide potential explosion mitigation measures e.g. explosion vents / panels so as to reduce the source explosion overpressure.
Dispersion Modelling
Gas dispersion is a process where gas accumulated (cloud formation) in confined space. Gas dispersion is mainly depending on gas/liquid release leak size, leak direction/wind direction, ventilation rate, ignition location & release timing. In CFD analysis gas dispersion model is developed by considering all possible cases (leak location & leak size) & find out most confined area where maximum gas cloud is developed.
Ventilation Modelling
A ventilation Computational Fluid Dynamics (CFD) model shows the flow of air and heat within a building. By comparing air intake and exhaust, CFD modeling can be used to design more effective and efficient ventilation systems. It is especially useful at pinpointing temperatures at different locations and elevations throughout a facility. Computational Fluid Dynamics (CFD) modeling to predict air flows distribution, heat levels and energy distribution also more accurately determine where the ideal quantity and locations for the ventilators.
Fire, Smoke Modelling, and evacuation
Techniche engineering work on effectiveness of a smoke exhaust system in a complex building using the Computational Fluid Dynamics (CFD) models. The Smoke movement from the origin of fire in the lobby and smoke contamination in the interconnected corridors are simulated in order to design the exhaust system to be capable of maintaining tenable conditions in the corridor used for e
Fire and Gas Mapping
A well-designed fire and gas system provides an appropriate level of redundancy to guard against false trips and detector faults. Computational Fluid Dynamics (CFD) is helpful to determine the gas dispersion, cloud formation, radiation, flame length, flame area etc. across a process area. CFD study improve the fire and gas detectors and relocating some of the originally proposed/ existing gas detectors.
 Solutions.jpg)
Air Quality Impact assessment
Air quality and pollution dispersion analysis can be undertaken to investigate the dispersion of exhaust gases from proposed or existing developments or nearby high-density processes plant. These types of analysis are particularly important where the emitted gas or pollutant is considered harmful to those exposed to it for any length of time. Further, these studies can investigate whether exhaust gases or pollutants are likely to linger within or propagate to critical outdoor areas or be re-circulated though the fresh air-intakes of HVAC systems, all of which could create undesirable or unsafe conditions. All such scenarios are analyzed with the help of computational fluid dynamics.
Air quality dispersion poses a wide range of challenges to designers, but a few examples are listed below:
- Noise Predictions
- Assessment of exhaust gas dispersion and exhaust velocities inside building, plant, public sector.
- Odor propagation analysis from various sources including Sewerage or Chemical Plants from which Hydrogen Sulfide is emitted.
- Smoke Dispersion from power plants or industrial facilities.
Wind Tunnel Analysis
The wind tunnel is proper functioning platform for accurate aerodynamic research which helps to provides adequate environment condition around scaled model to the compatible dimension. In order to understand the physical phenomena of the wind flow over the typical launch vehicle, the flow was simulated using both Wind tunnel and Computational Fluid Dynamics (CFD) & generated data is used to validate the experimental results & modification in design.
CFD for Refining Processes
Computational Fluid Dynamic (CFD) modelling has been widely used for a relatively short period in the refining and petrochemical industries for modelling process heaters, fired furnaces and other combustion equipment such as thermal oxidizers, slug catcher, heat exchanger and ground flares etc. to analysis the effect of various processing fluid.
CFD Analysis of Dam Break
Dam breaks can cause rapid floods downstream, with catastrophic consequences in terms of loss of lives and damages of properties and natural habitats, which can be minimized by forecasting the hazards. The dam-break wave propagation usually occurs over a downstream bottom with irregular topography, resulting for example from natural contraction-expansion and meandering of river channels and presence of artificial (buildings, bridges) or natural (debris, dikes, trees) obstacles. The commercially available CFD program used for the numerical simulations of the same scenarios observed during in real environment. Simulation predict the stresses generated on dam due to back water & provide flow behavior after dam break.
CFD analysis of fire sprinkler system and evacuation
Dam breaks can cause rapid floods downstream, with catastrophic consequences in terms of loss of lives and damages of properties and natural habitats, which can be minimized by forecasting the hazards. The dam-break wave propagation usually occurs over a downstream bottom with irregular topography, resulting for example from natural contraction-expansion and meandering of river channels and presence of artificial (buildings, bridges) or natural (debris, dikes, trees) obstacles. The commercially available CFD program used for the numerical simulations of the same scenarios observed during in real environment. Simulation predict the stresses generated on dam due to back water & provide flow behavior after dam break.
Modeling and Analysis of Flare Stack Thermal Radiation
Flare stacks are the arrangement that are used to burn the combustible gases that are released out of the pressure relief valves and the over-pressurized equipment in industries such as petroleum, petrochemical and chemical industries. These gases can lead to hazardous effects on the environment if vented without complete combustion. Besides, the combustion of these vapors and gases also generate thermal radiation. With the increasing environmental responsibilities and societal concerns and with increasing corporate responsibility to comply with the ever stringent environmental laws, it has become essential to perform the CFD flare radiation and dispersion studies to assess and minimize the release of toxic/hazardous gases into the environment.
Fire Scenario Assessment for Metro Station
Metro & rail both applications need ventilation rates. In Metros the influx of many people and the presence of moving trains generate a reduction of oxygen and an increase in heat and pollutant. Mechanical ventilation is then required to achieve the necessary air exchange which will provide users comfortable conditions. Ventilation systems have a second and even more important purpose. That is to guarantee safety in case of fire emergency. In order to create a safe and clean environment for escaping, mechanical ventilation both in tunnels and in the stations is activated. In rails the ventilation of tunnels is mainly dedicated to fire emergencies where it is vital to keep under control the smoke propagation and create safe areas and clear environment for the users.
We offer operation and maintenance services for,
CFD analysis of Pipelines Sampling System
In oil & gas industry pipeline is the most cost effective, energy efficient, safe and environment friendly mode of transportation of petroleum products. In CFD analysis flowing fluids are expected to be multiphase i.e. mixture of gas-liquid-solid flowing through pipelines on which sampling systems to be installed. A sampling prob is inserted inside the flowing stream to collect sample into receiver. It is important to fix sampling point where turbulence is enough to ensure good mixing to obtain sample. CFD analysis is to be done at each sampling point to verify flow distribution & corrosion effect.
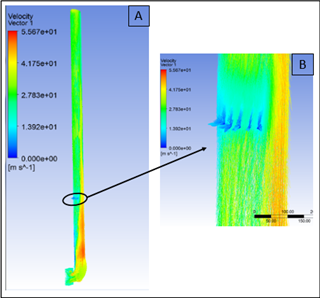
CFD Analysis for Gas Oil Separation System
Variations in oil properties or the water content influence crude oil-water separation thereby posing challenges for separator operations when conditions change as the fields mature and in the design of new internals to improve separation efficiency. Computational fluid dynamics (CFD) is being used to predict separator vessel hydrodynamics and the studies of three-phase (oil-water-air) separators phenomena and provide some useful guidelines for optimization design also helpful to increase efficiency.
We offer operation and maintenance services for,
Ship Collision Assessment
Ship Collision Study is to assess the risks and hazard of collision between ships and offshore installations including wellhead platforms. The CFD study will identify the causes of collision and the model of evaluating the risk involved in the collision. The identified causes will be briefly discussed and proposing the suggestions to reducing such risks.
Common factors in ship collision
- Speed & displacement of the Colliding ship.
- Environmental conditions like rogue waves, high speed wind
- Design of ship’s structure & its capacity to bear collision.
- Unawareness of existence of platform / FPSO.
- Human errors like watch keeping failure, erroneous actions.
- Equipment like radar failure..
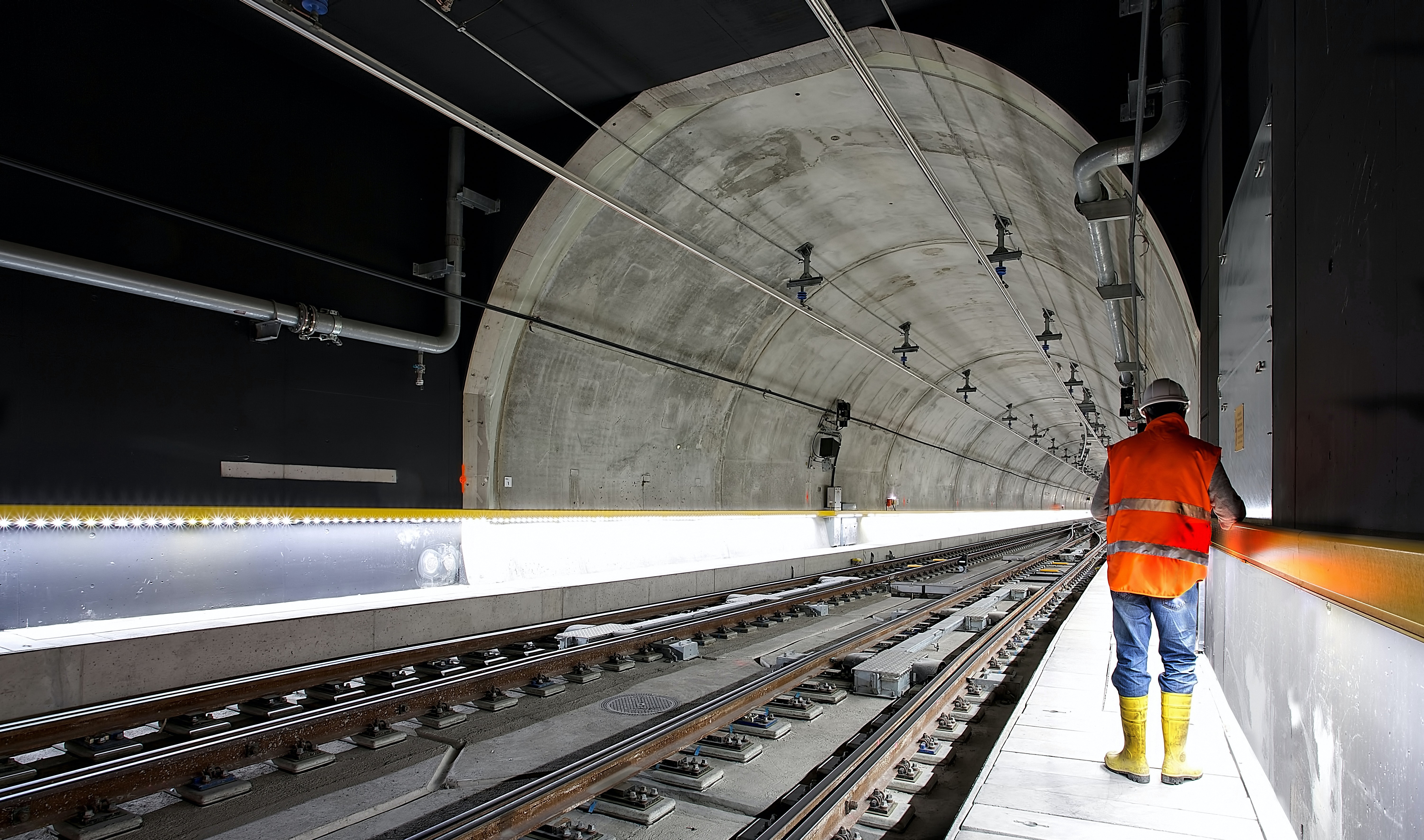
Finite Element Analysis (FEA)
Finite element analysis (FEA) is the process of simulating the behavior of a part or assembly under applied boundary conditions. FEA is the practical application of the finite element method (FEM), which is used by engineers and scientists to mathematically model and numerically solve complex structural and Multiphysics problems.
Our FEA consulting engineers having expertise’s in-
Static Analysis
Static analysis is widely used and only be performed if the system being simulated does not depend on time, and if the loads being applied are constant. This study investigate deformation, stress and strain of an assembly or a component, for a range of loads which ensures structural integrity of the system.
Linear Analysis
A linear static analysis is an analysis where a linear relation holds between applied forces and displacements. In practice, this is applicable to structural problems where stresses remain in the linear elastic range of the used material. In a linear static analysis, the stiffness matrix is constant, and the solving process is relatively short compared to a nonlinear analysis on the same model.
Nonlinear Analysis
A nonlinear analysis is an analysis where a nonlinear relation holds between applied forces and displacements. Nonlinear effects can originate from geometrical nonlinearity’s (i.e. large deformations), material nonlinearity’s (i.e. elasto-plastic material), and contact.
Modal Analysis
Modal analysis is used to identify natural frequencies and their vibration modes. Every structure has its own natural frequencies. When the excitation of a vibration on a machine coincide with a natural frequency of the system, the structure resonance with the excitation force which lead to excessive sometimes violent vibrations, which may lead to damage of the structure. A dynamic loading on a machine will introduce vibrations. The excessive vibrations will cause noise, lead to fatigue damage of the components. Vibrations in a vehicle will make passengers uncomfortable and lead to tiredness.
Harmonic Response Analysis
A follow on from modal analysis, harmonic analysis allows the evaluation of the part response to actual expected dynamic loads. E.g. stress, deflection and fatigue life of a part can be predicted based on dynamic loading.
Transient Dynamic Analysis
This analysis determines the response of the part due to loads that are a function of the time – like harmonic response except the loading can be non-periodic.
Multibody (rigid) Dynamic Analysis
A multibody dynamic (MBD) system is one that consists of mutually interconnected multiple rigid bodies, or links, that are connected to each other by joints that restrict their relative motion. The study of multibody dynamics analysis is the analysis of how mechanism systems move under the influence of forces.
Thermal Analysis
Temperature distribution and loads are often required to understand the system working under elevated temperature which can lead to high thermal stresses and strains which may cause for component failure that can be analyzed using thermal analysis.
Fatigue Analysis
Fatigue is failure under repeated or otherwise varying load which never reaches a level sufficient to cause failure in single application & develops cyclic stresses which lead to major failures in component.
High Cycle Fatigue
In high-cycle fatigue situations, materials performance is commonly characterized by an S-N curve, also known as a Wohler curve. This is a graph of the magnitude (or stress range) of a cyclic stress (S) against the logarithmic scale of cycles to failure (N). The progression of the S-Ncurve can be influenced by many factors such as corrosion, temperature, residual stresses, and the presence of notches.
Low Cycle Fatigue
For most real-world components, the nominal stresses remain elastic, but occasional high loads and stress concentrations cause plastic deformation. Fatigue damage is controlled by the local plastic strains. When the stress is high enough for plastic deformation to occur, the accounting of the loading in terms of stress is less useful and the strain in the material offers a simpler and more accurate description. This is called low cycle fatigue, which uses a so-called E-N curve instead of an S-N curve. The Strain Life Relation Equation is constructed from two separate curves (one for elastic life and one for plastic life).